When it comes to HVAC systems, the choice between alternating current (AC) and direct current (DC) motors can significantly affect efficiency, performance, and cost. Understanding the differences between these two types of motors is essential for engineers, technicians, and even end-users who want to make informed decisions about their HVAC systems.
AC Motors: The Workhorse of HVAC Systems
How AC Motors Work
AC motors are powered by alternating current, which changes direction periodically. This type of motor uses electromagnetic induction to convert electrical energy into mechanical energy. The key components of an AC motor are the stator (the stationary part that generates a rotating magnetic field) and the rotor (the rotating part that is affected by the magnetic field). The interaction between the stator's magnetic field and the rotor causes the rotor to turn, thus creating mechanical power.
AC Motor Types
AC motors, essential to many applications across various industries, are divided into two primary types based on their operational principles: induction (asynchronous) motors and synchronous motors. Each type has unique characteristics and is suited for specific applications.
Induction Motors (Asynchronous Motors)
Induction motors operate on the principle of electromagnetic induction, where the rotor (the moving part) is induced by a magnetic field created by the stator (the stationary part). This type of motor does not require electrical connections to the rotor; instead, the rotating magnetic field produced by the AC in the stator induces a current in the rotor, causing it to rotate.
Induction motors are further divided into:
- Squirrel Cage Induction Motors: The most common type, known for their rugged construction and simplicity. The rotor consists of aluminum or copper bars (resembling a squirrel cage) short-circuited by rings at both ends.
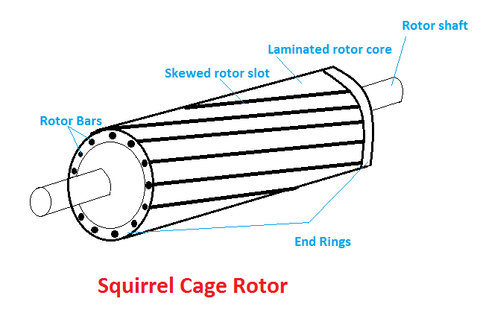
- Wound Rotor Induction Motors: These motors have a rotor winding connected through slip rings to external resistances for starting and control. They offer better control over starting current and speed adjustments.
Synchronous Motors
Synchronous motors operate at a constant speed up to their full load and synchronize with the supply current frequency; the magnetic field's rotation period in the stator winding is equal to the rotation period of the rotor. They are divided into:
- Non-Excited Motors: These motors use permanent magnets, reluctance, or hysteresis in the rotor to maintain synchronization with the stator's magnetic field. They are typically used in lower-power applications.
- Excited Motors: These have windings in the rotor that are excited by an external DC source or by using slip rings and brushes. Excited synchronous motors can operate at very high power levels and are used in applications requiring precise speed and position control.
AC Motor Applications & Selection
- Induction Motors: Preferred for general-purpose applications due to their simplicity, reliability, and low cost. They are widely used in industrial drives, household appliances, and HVAC systems.
- Synchronous Motors: Ideal for applications where constant speed is necessary, regardless of load changes. They are used in precision timing devices, high-capacity industrial drives, and power generation plants.
The choice between an induction and synchronous motor depends on specific application requirements such as speed control, efficiency, cost, and maintenance. Induction motors are favored for their ease of use and maintenance, while synchronous motors are chosen for their precision control and efficiency at constant speeds.
DC Motors: Efficiency & Control
How DC Motors Work
DC motors are powered by direct current, which flows in one direction. These motors convert electrical energy into mechanical energy through the interaction of a magnetic field generated by a stationary part (the stator) and a rotating part (the armature or rotor). The direction of the current in the rotor is switched periodically by a commutator, causing the rotor to rotate.
DC Motor Types
DC motors are vital components in many applications, offering precise control over speed and torque. There are several types of DC motors, each with unique characteristics and applications. The primary types include:
Brushed DC Motors
These motors operate with brushes that conduct current through the commutator to the rotor winding, generating a magnetic field that drives the motor. Brushed DC motors are known for their simplicity and ease of control but require more maintenance due to brush wear.
- Advantages: Simple control for speed and torque, lower initial cost.
- Applications: Automotive starters, small appliances, power tools.
Brushless DC Motors (BLDC)
BLDC motors eliminate the need for brushes by using an electronic controller to switch the phase to the stator coils. This generates a rotating magnetic field that interacts with the rotor, improving efficiency, reducing maintenance, and increasing lifespan.
- Advantages: High efficiency, reliability, longer lifespan, and low maintenance.
- Applications: Electric vehicles, drones, HVAC applications, and industrial machinery.
Stepper Motors
Stepper motors are DC motors that move in discrete steps, allowing precise control of position and speed. Each pulse of current moves the rotor in fixed steps. Stepper motors are widely used in applications requiring precise positioning.
- Advantages: Precise positioning and repeatability, easy to control in an open loop system.
- Applications: 3D printers, CNC machines, robotics.
Servo Motors
Servo motors are a specialized type of DC motor combined with a sensor for position feedback, controlled through a closed-loop system. Servo motors can control speed, position, and torque very accurately.
- Advantages: Precise control of position, speed, and torque, as well as high efficiency.
- Applications: Robotics, antenna positioning, automated manufacturing systems.
Each type of DC motor offers distinct advantages and is suited for specific applications based on speed, torque, control precision, and maintenance requirements. Brushed motors are chosen for their simplicity and low cost for basic applications, while brushless motors are preferred for their efficiency and low maintenance in more demanding applications. Stepper and servo motors provide high precision and are ideal for applications where accurate positioning is critical.
AC vs. DC Motors in HVAC: What to Choose?
The choice between AC and DC motors for HVAC applications depends on several factors, including energy efficiency requirements, cost constraints, and the need for speed control. AC motors are generally more cost-effective and suitable for standard HVAC applications. However, DC motors, particularly BLDC motors, are the better choice for applications requiring high efficiency and precise speed control despite their higher initial cost.
FAQs: AC vs. DC Motors
Which is more efficient, AC or DC motors?
DC motors, especially BLDC motors, are typically more efficient than AC motors. This is because they can operate at higher speeds with less power loss.
Are DC motors more expensive than AC motors?
Yes, DC motors, especially brushless DC motors, are generally more expensive upfront than AC motors due to their complex construction and control systems. However, the higher efficiency and lower maintenance costs of DC motors can offset the initial investment over time.
Can I replace an AC motor with a DC motor in my HVAC system?
While it is technically possible to replace an AC motor with a DC motor, this requires careful consideration of power supply, control systems, and compatibility with the existing HVAC system. It's advisable to consult with an HVAC professional before making such a switch.
Which motor type is better for residential HVAC systems?
AC motors are sufficient for most residential HVAC systems, offering a good balance between cost and performance. However, due to their superior efficiency and control capabilities, DC motors may be the preferred choice for high-efficiency or smart HVAC systems.
Which motor type is better for commercial HVAC systems?
In commercial HVAC systems, brushless DC (BLDC) motors are increasingly favored due to their high efficiency, superior speed control, longevity, low maintenance, and quieter operation. These advantages make BLDC motors particularly suitable for the diverse needs of commercial environments, where energy savings, precise climate control, durability, and comfort are paramount.