Compressors are pivotal in refrigeration, ensuring the environment remains at the desired temperature. The heart of this process is the compressor duty motor, a robust and specialized motor designed to meet the rigorous demands of running a compressor.
What is a Compressor Duty Motor?
A compressor duty motor is specifically designed to meet the demanding requirements of air compressor applications. These motors are engineered to handle high torque and start-up loads associated with starting and running compressor units, which often require significant power to overcome the initial pressure build-up in the compressor system.
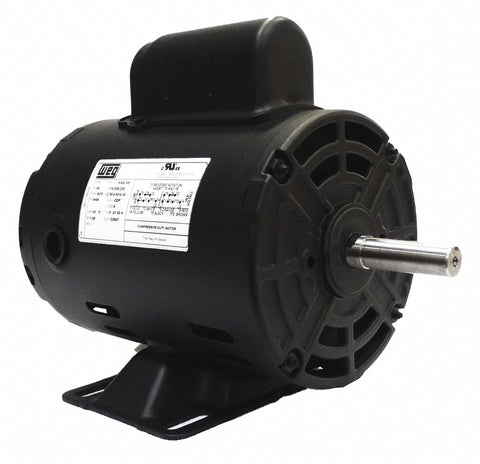
Compressor duty motors are commonly used in both residential and industrial air compressor systems, ranging from small, portable units to large, stationary installations. They are essential for ensuring that the compressor operates efficiently, safely, and reliably over its lifetime.
Compressor Duty Motor Features
-
High Starting Torque: Compressor duty motors have a high starting torque to drive the compressor load from a standstill to operational speed. This is crucial because air compressors typically require substantial force to start, especially in systems with high pressure or when loaded.
-
Durability & Reliability: These motors are built to withstand the rigorous conditions of compressor operation, including vibration, temperature fluctuations, and continuous or frequent start-stop cycles. The materials and construction are chosen for their durability and ability to perform reliably over time.
-
Efficiency: While efficiency can vary across models, many compressor duty motors are designed to operate efficiently to reduce electrical consumption and operational costs. This is particularly important in industrial applications where compressors run for extended periods.
-
Thermal Protection: Overheating is a common concern with motors under heavy loads, so compressor duty motors often include thermal protection features. These can be built-in thermal overload protection or external devices that monitor the motor's temperature and reduce the risk of overheating.
-
Service Factor: These motors typically have a high service factor, meaning they can handle temporary overload conditions beyond their nominal rating without damage.
-
Cooling: Effective cooling mechanisms, such as external fan cooling, are critical for maintaining the motor's temperature within safe operating limits.
How Do Compressor Duty Motors Work?
Starting the Compressor
- High Starting Torque: When the motor is turned on, it must overcome the initial inertia and any system pressure in the compressor. Compressor duty motors are designed to provide high starting torque to accomplish this. This is often achieved through specific electrical and mechanical designs that allow the motor to generate a greater force at start-up.
- Electrical Windings: The windings of a compressor duty motor are designed to ensure that the motor can start under load. This involves using thicker wire or different materials to handle the high current during startup without overheating.
Running the Compressor
- Energy Conversion: Once the motor starts, it converts electrical energy into rotational mechanical energy. This involves inducing a magnetic field in the motor's windings to create rotation, which is then transferred to the compressor's pump mechanism through a shaft.
- Continuous Operation: Compressor duty motors are built to sustain continuous operation without overheating. This is managed through efficient electrical designs, materials that dissipate heat effectively, and cooling systems (like fans) that maintain a safe operating temperature.
- Thermal Protection: These motors are equipped with thermal protection mechanisms to prevent damage from overheating. These can be thermal overload relays or built-in thermal protectors that shut down the motor or reduce its load when temperatures exceed safe levels.
- Efficiency & Power Management: During operation, the motor adjusts to the demands of the compressor load. This can involve varying the power output to match the load requirements, optimizing efficiency, and reducing electrical consumption.
Handling Load & Overload Conditions
- Service Factor: Compressor duty motors have a service factor rating that allows them to operate above their nominal power for short periods without damage. This is important for handling situations where the compressor requires a sudden increase in power, such as when compressing air into a tank nearing total capacity.
- Robust Construction: The physical construction of these motors is robust to withstand the vibration, pressure fluctuations, and environmental conditions typical in compressor applications. This includes using durable materials and bearings designed for high-load applications.
Sizing a Compressor Duty Motor
Selecting an appropriately sized compressor duty motor is crucial for an air compressor system's efficient and reliable operation. The process involves understanding the compressor's power requirements and operating conditions. Here are the key steps and considerations for sizing a compressor duty motor:
Determine the Compressor's Power Requirement
- Compressor Type & Application: Identify the type of compressor (e.g., reciprocating, rotary screw, centrifugal) and its application (e.g., industrial, HVAC, automotive). Different types have different power needs.
- Required Airflow & Pressure: Calculate your application's airflow (CFM, cubic feet per minute) and pressure (PSI, pounds per square inch) requirements. This will help you understand the load the compressor needs to handle.
Calculate the Required Power
- Compressor Efficiency: Consider the efficiency of the compressor mechanism itself. Manufacturers typically provide this information. Inefficiencies mean that the motor will need to supply more power than the theoretical minimum to achieve the desired airflow and pressure.
- Power Formula: Use the appropriate formula for calculating the required power (in horsepower or kilowatts) based on the airflow, pressure, and compressor efficiency.
Consider Starting Torque
- High Starting Load: Compressor duty motors often need to start under load, especially if the system doesn't fully unload during shutdown. Ensure the desired motor has high starting torque to overcome the initial resistance.
Factor in Service Factor
- Service Factor: Look at the motor's service factor, which indicates how much over its rated power the motor can operate for short periods. A higher service factor provides a buffer for unexpected loads or conditions but should not be used to run the motor above its rated power perpetually.
Assess Duty Cycle
- Duty Cycle: Understand the compressor's expected duty cycle. If the compressor runs continuously or cycles on and off frequently, the motor needs to be durable and capable of handling these conditions without overheating.
Environmental & Operational Conditions
- Ambient Temperature: Consider the temperature where the motor will operate. High temperatures can reduce motor efficiency and lifespan.
- Altitude: Higher altitudes can affect motor performance due to lower air density for cooling.
- Cooling Requirements: Ensure the motor's cooling system (often a built-in fan) is adequate for your application’s environmental conditions.
Safety Margins and Future Needs
- Add a Safety Margin: After calculating the required motor size, add a safety margin (e.g., 10-20%) to ensure the motor can handle unexpected increases in load or system inefficiencies.
- Future Expansion: Consider any potential future increases in demand on the compressor system. Installing a slightly larger motor now might be more cost-effective than upgrading the entire system later.
Professional Guidance
- Consult with Manufacturers or Specialists: Because of the complexity and the critical nature of sizing a motor correctly, it’s often wise to consult with motor manufacturers or engineering specialists. They can provide valuable insights and confirm whether your calculations and assumptions are appropriate for your application.
Following these steps helps ensure that the compressor duty motor you select can meet the operational demands of your compressor system and provide efficient, reliable service over its intended lifespan.
FAQs
Can I replace a compressor duty motor with a standard motor?
It's not recommended. Standard motors may not have the necessary starting torque or cooling mechanisms to handle the demands of a compressor, leading to inefficiency or failure.
How often should a compressor duty motor be replaced?
The lifespan of a compressor duty motor varies based on usage, maintenance, and the environment. Regular maintenance checks can identify potential issues before failure, but these motors typically last several years under normal conditions.
How do you replace a compressor duty motor?
First, ensure safety by disconnecting the power and wearing protective gear to replace a compressor-duty motor. Document the old motor's setup before removal, especially if it's belt-driven. Ensure the new motor matches the original in horsepower and voltage. Install the new motor, carefully reconnect electrical wiring based on your notes, and adjust belt tension if necessary. Before powering up, manually check for any issues by rotating the shaft. Once powered, monitor the compressor for smooth operation and proper function. Secure all wiring and update your documentation with the new motor's details. Seek professional assistance if unsure and ensure compliance with local codes.
What maintenance is required for compressor duty motors?
Regular maintenance includes checking for overheating, ensuring the cooling system is functioning properly, and verifying that the motor is running efficiently without unusual noises or vibrations.
Are compressor duty motors energy efficient?
Yes, many are designed with energy efficiency in mind. However, efficiency can vary depending on the specific model and its usage. To reduce energy consumption, always look for motors with high-efficiency ratings.
What causes high motor heat on a suction-cooled compressor?
High motor heat in suction-cooled compressors primarily results from inadequate cooling due to low suction pressure, high ambient temperatures, or insufficient ventilation. Electrical issues like overloading, mechanical friction from worn bearings or misalignment, and high compression ratios due to dirty condenser coils or refrigerant problems can also contribute to overheating. Furthermore, frequent cycling and blockages in suction filters or screens restrict the refrigerant flow needed for cooling. Addressing these issues involves maintaining proper refrigerant levels, ensuring clear suction pathways, and checking electrical and mechanical components for faults. Regular maintenance is critical to preventing overheating and ensuring efficient compressor operation.
How to tell if an air compressor motor is bad?
To determine if an air compressor motor is bad, look for signs such as failure to start, overheating, unusual noises like grinding or humming, circuit breakers frequently tripping, a burning smell, excessive vibration, and visible physical damage. Weak or intermittent operation can also indicate motor issues. For a more detailed diagnosis, you can perform electrical tests using a multimeter to check for continuity in the motor windings or test capacitors if applicable. However, if these signs are present or you're unsure about conducting these tests, it's best to consult a professional technician to assess whether the motor needs repair or replacement.
This video from Nidec shows an application stress test on a compressor motor:
What is the minimum size disconnecting means allowed for a hermetic refrigerant compressor motor?
The minimum size of the disconnecting means for a hermetic refrigerant compressor motor is guided by the National Electrical Code (NEC), specifically Article 440, which suggests that the disconnect size should be no less than 115% of the compressor's nameplate-rated load current or branch-circuit selection current, whichever is greater. This requirement ensures the disconnect can safely handle the motor's electrical demands during operation. It's crucial to consult the latest NEC version and local codes for the most accurate requirements, as these can vary by jurisdiction and are updated periodically. Speaking with a qualified electrical professional is recommended for detailed and compliant installations.
By what means does a two-speed compressor motor accomplish a speed change?
A two-speed compressor motor typically accomplishes a speed change by using different winding configurations or altering the power supply frequency. In a dual-winding configuration, the motor has separate windings for high and low speeds, with the switch between the two being controlled by a relay or electronic controller based on the cooling demand. Alternatively, in systems using variable frequency drives (VFDs), the speed change is achieved by electronically varying the frequency of the electrical power supplied to the motor. This allows the motor to run at different speeds by changing the rate at which the electrical current is cycled, providing precise control over the compressor's output to match the cooling or heating requirements efficiently.
Why are starting components needed on a single-phase compressor motor?
Starting components are needed on a single-phase (1Φ) compressor motor because such motors inherently lack the phase shift necessary to create a rotating magnetic field, which is essential for starting and running the motor. These components, typically a start capacitor combined with a start relay or a potential relay, temporarily introduce an additional phase shift at start-up. The start capacitor boosts the initial starting torque by providing a higher current to one of the windings, creating a stronger and more distinct phase difference. Once the motor reaches a certain speed, the relay disconnects the start capacitor from the circuit, allowing it to run on its main winding. This system ensures the motor starts efficiently and effectively, overcoming initial inertia and reducing the electric load that would otherwise be required to start the motor directly from the power line.
What is the purpose of an internal overload protector in a compressor duty motor?
An internal overload protector safeguards the motor from damage due to overheating, which can result from excessive current, prolonged operation under high loads, or insufficient cooling. This protective device is sensitive to the motor's temperature and automatically interrupts the electrical circuit if the motor overheats, preventing potential damage to the motor's windings and other components. Depending on its design, once the motor cools down to a safe operating temperature, the overload protector can either reset automatically or require manual resetting. This ensures the motor's longevity and reliability by protecting it against conditions that could lead to premature failure.
How do you tell if a slow-starting air compressor is due to the motor or pump?
You can perform a few diagnostic checks to determine if a slow-starting air compressor is due to the motor or the pump. Firstly, listen for unusual noises or observe excessive vibration, which may indicate mechanical issues with the pump, such as seized bearings or internal friction. Secondly, disconnect the pump from the motor and attempt to start it alone; if it starts promptly and runs smoothly without the pump connected, the issue likely lies with the pump. Conversely, suppose the motor starts slowly or exhibits signs of struggle when disconnected from the pump. The problem may be related to the motor, potentially involving electrical issues such as weak capacitors, worn windings, or an overloaded electrical circuit. This process helps isolate the component causing the slow start, allowing for targeted troubleshooting and repairs.